At our company, we have had the privilege of working with one of the most renowned oil and gas industry leaders in Malaysia, completing a significant project involving pipe stress analysis for LNG lines using CAESAR II software. Pipe stress analysis is a critical testing method that examines the behavior of a piping system under various loading conditions. In this article, we will share our project experience and highlight the importance of pipe stress analysis in ensuring the safety and reliability of oil and gas operations.
Project Overview:
Our team successfully completed the analysis of pipe stress in the project, thoroughly examining how the piping system responded to crucial loads including weight, pressures, temperatures, displacements, forces, and restraints. Through comprehensive analysis, we were able to assess the flexibility, stiffness, and overall performance of the piping system, providing valuable insights to our client.
Key Benefits of Pipe Stress Analysis:
Observing Pipe Behaviour: Our project involved closely observing the flexibility and stiffness of the piping system, allowing us to gain a deep understanding of how they respond to different operating conditions. This knowledge enabled us to make informed decisions regarding the design and structural integrity of the piping system.
Determining Critical Parameters: By conducting pipe stress analysis, we were able to determine crucial parameters, such as overstresses, maximum stresses, forces, moments, and displacements. Due to the helpful feature of CAESAR II, the findings could be analysed in two different formats namely graphical and tabular/numerical as shown in Figure 1 and Figure 2, respectively. These findings were vital in identifying potential weak points in the piping system and ensuring compliance with applicable standards.
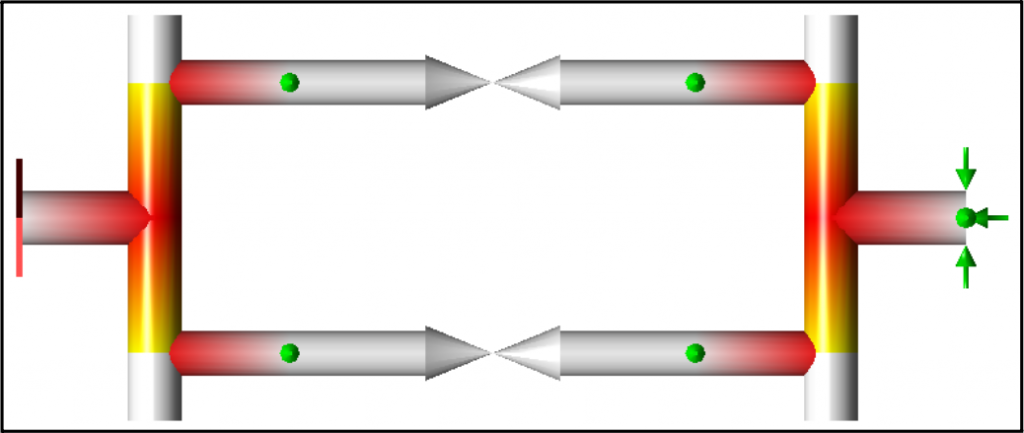
Figure 1: Overstressed in the piping system is illustrated by the red spots (The image is used as an illustration purpose only and not related to the real project due to P&C)
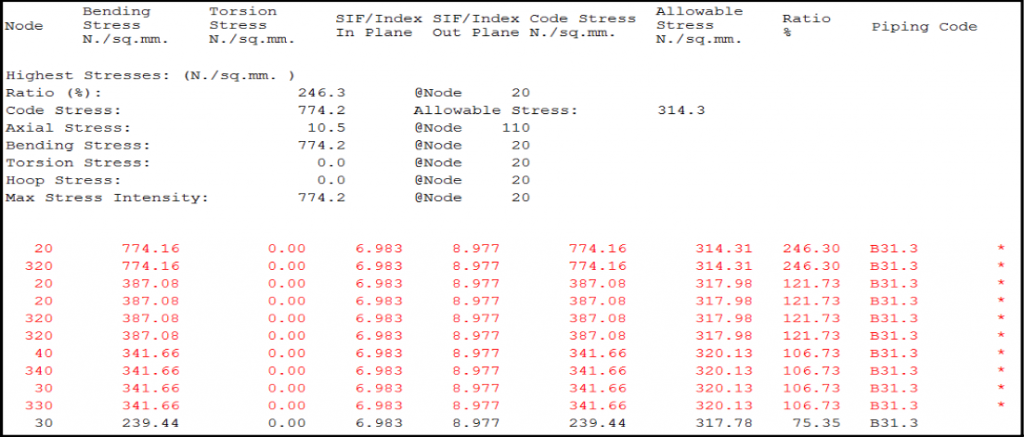
Figure 2: Red-highlighted lines indicates overstressed in the piping system (The image is used as an illustration purpose only and not related to the real project due to P&C)
Selecting Suitable Support Systems: The accurate selection of support systems is crucial to maintainin the integrity of a piping system. Our analysis results guided us in choosing the appropriate support systems that effectively handled the loads and movements of the pipes, thereby minimizing the risk of failures.
Detecting and Preventing Issues: Pipe stress analysis allowed us to identify potential disengagements from support structures and pipes, enabling us to take proactive measures. Additionally, we could anticipate and address mechanical vibrations, seismic loads, or acoustic vibrations that might have influenced the pipe operations, ensuring a safe working environment.
Ensuring Leak-proof Systems (Flange Checks): As part of our project, we conducted thorough pipe stress analysis for the LNG lines, which are critical for the transport of hazardous materials. This analysis helped us ensure the structural integrity of the pipes, minimizing the risk of leaks and potential accidents.
Importance of Pipe Stress Analysis:
Pipe stress analysis is recommended in various scenarios to maintain the safety and reliability of piping systems. Our experience has shown that pipe stress analysis is particularly crucial when:
- Operating temperatures are 150°F or higher, as thermal expansion and contraction can significantly impact the system's integrity.
- Pipe or line sizes are 4' or above, or when line sizes of 2 ½" and above are involved with rotating equipment.
- Pressure vessels are connected, requiring analysis for line sizes of 6" and above.
- Complex systems with multiple branches are present, necessitating a detailed analysis to ensure proper support and avoid stress concentrations.
- A lack of flexibility is detected within the piping system, indicating potential issues due to restricted movement (Piping system is too stiff).
- The system is subjected to vibrations, such as during suction or discharging operations.
- The plant is located in an area with high seismic activity, demanding robustness against seismic loads.
Conclusion:
Our successful project with the esteemed oil and gas industry leader in Malaysia highlighted the importance of pipe stress analysis in ensuring the safety and reliability of piping systems. By conducting comprehensive analyses, we were able to provide valuable insights into the behaviour of the pipes under various operating conditions. This experience reinforced the significance of pipe stress analysis in making informed decisions, mitigating risks, and ensuring smooth operations in the oil and gas industry.